Introductions and Information
About Metal Injection Molding (MIM)
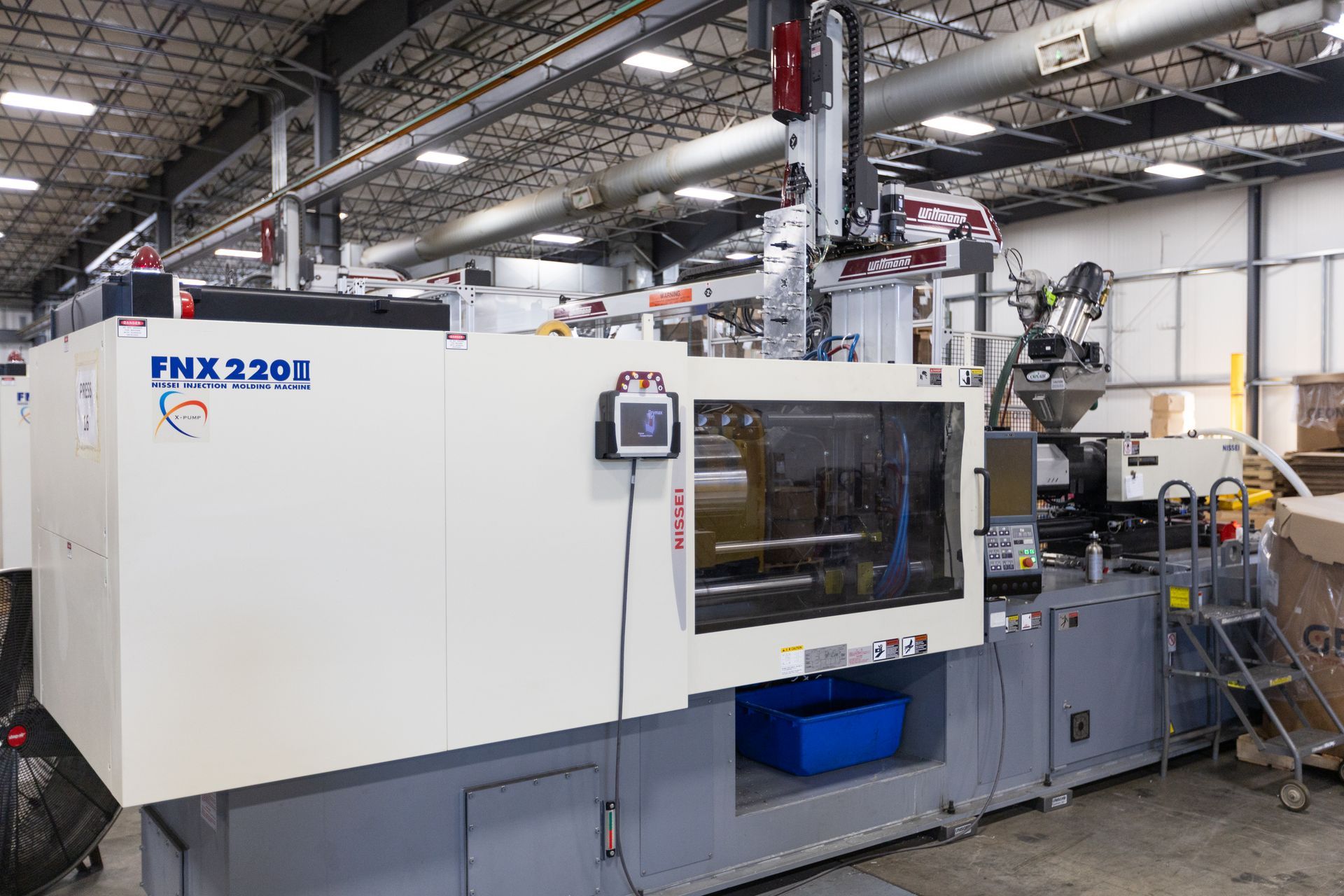
How do you know if your part is a good candidate for metal injection molding (MIM)? The first thing to think about is the quantity of parts you need. At Smith Metal Products, we work with customers looking for more than 25,000 parts per year if they have one design. For multiple designs, we look for over 10,000 parts per year for each design. Small runs of parts do not make sense for MIM with the cost of the molds needed for the process. The second determination depends on the material used to make the part. The typical metals we use at Smith Metal Products include stainless steel and titanium. However, there are many other alloys that we have experience with and others that we would be willing to develop depending on the scope of your project. We cannot use aluminum, zinc, magnesium, or brass. Part size can also dictate the compatibility with MIM. We look for maximum part lengths of three inches or less. However, there are some exceptions. Wall thickness (or thin-ness) may have an impact on MIM viability. The minimum wall thickness that we look for is .020" or 5 mm. We also do not want walls that are thicker than .125" or 3mm. In some cases, we may be able to "core out" these areas in the design for manufacturability process. Part weight is another consideration. Most of the parts we manufacture are under 25 grams, but we use 100 grams as the highest weight compatible with MIM. Why does it make sense to use MIM? If you have higher priced machined or cast components, MIM may be a cost savings. If you are a machine shop, MIM can be used to create blanks and free up machine time for you to work on other projects. Some multi-component assemblies may be combined into a single MIM component. Components made out of expensive materials like Inconel or titanium are good candidates since you do not cut away value material in the MIM process. The metal needed for the part is injected, not cut away from bar stock. If you are considering a part for MIM, please email us at DFM@smithmetals.com and we will evaluate the part.
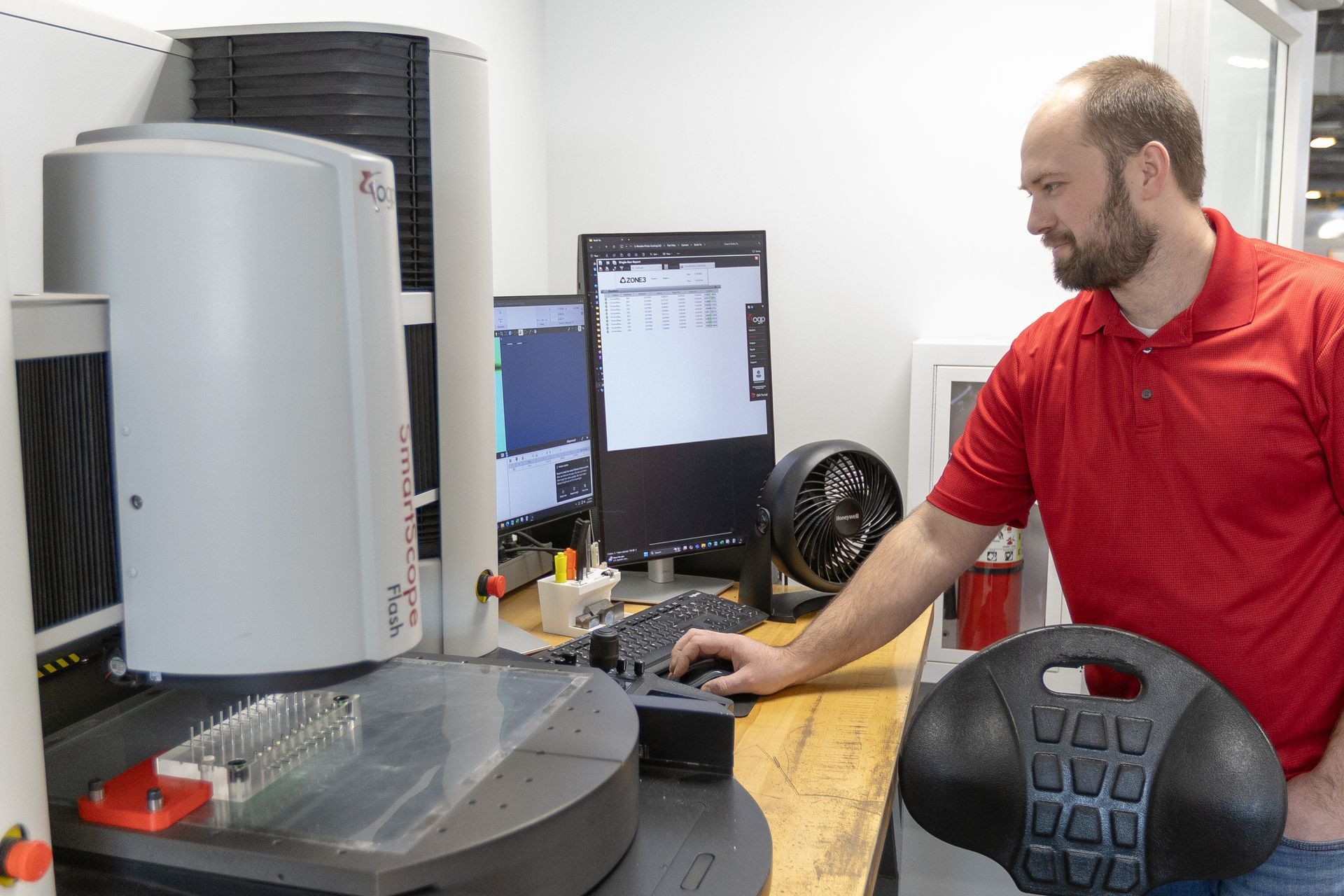
When you think about quality, what comes to mind? Meeting tolerances? Consistency? Free of defects? Strong, stable complex parts? All of these things come into play. Quality is important to us at Smith Metal Products. We want our customers to be glad they are working with us each and every time they place an order. We strive to meet or exceed all of our customers' requirements every day.
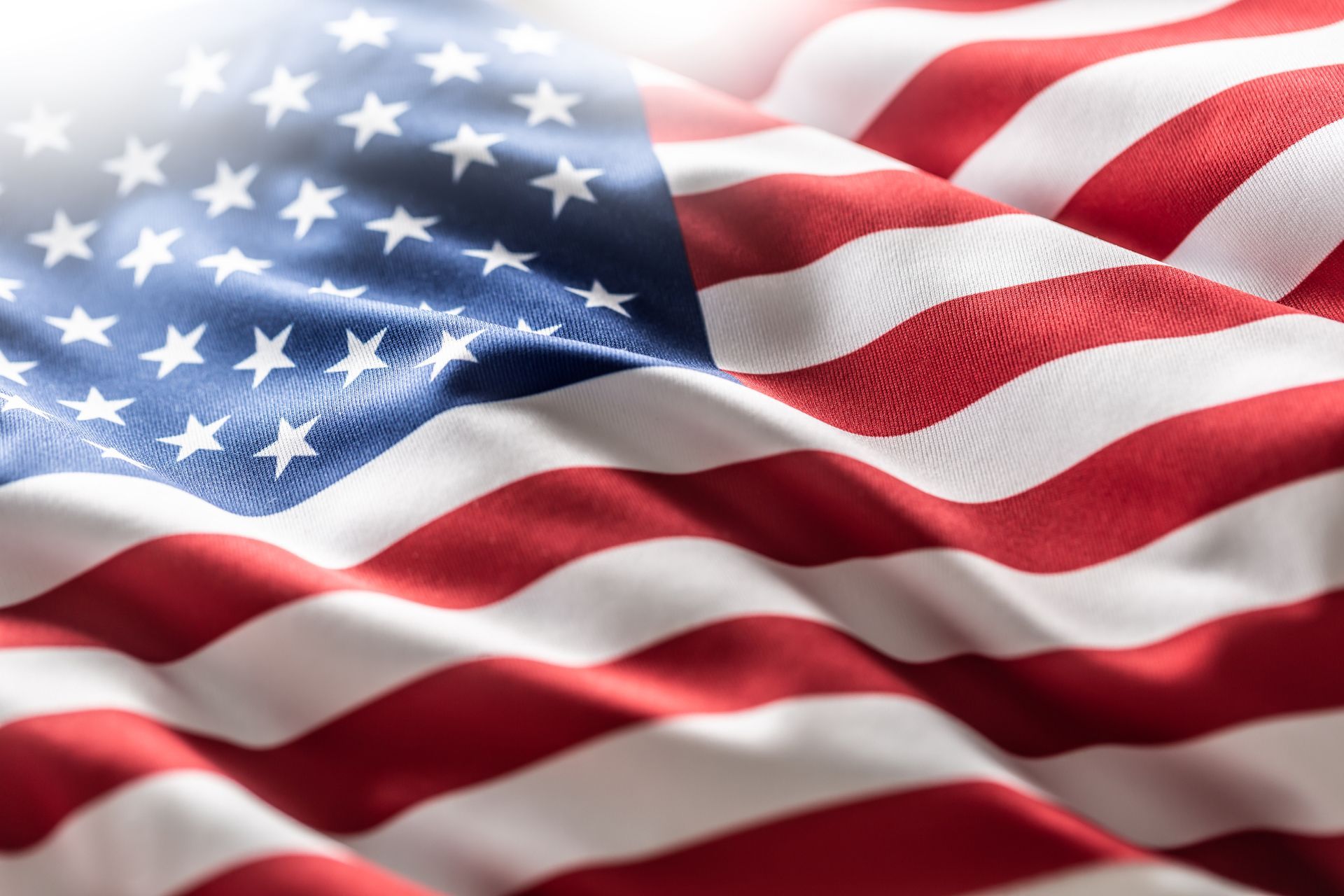
Smith Metal Products manufactures only in the United States. Located in Center City, Minnesota, Smith Metal Products in centrally located. Why is it beneficial to work with a company producing products only in America? 1. You support American jobs and local communities. 2. You reduce shipping times from your metal injection molding supplier. 3. Your parts won't get stuck and delayed in customs. 4. You can speak with the people that work right where your parts are being made and collaborate on design for manufacturability. 5. You don't have to worry about the uncertainty of tariffs, because you are not importing your parts. Some companies say they are manufacturing parts in their United States locations, and then have the designs made abroad. Rest assured that if you work with Smith Metal Products, your parts are being manufactured in Minnesota. If you would like to move your small, complex, high volume, metal part manufacturing back to the United States, email us at DFM@smithmetals.com
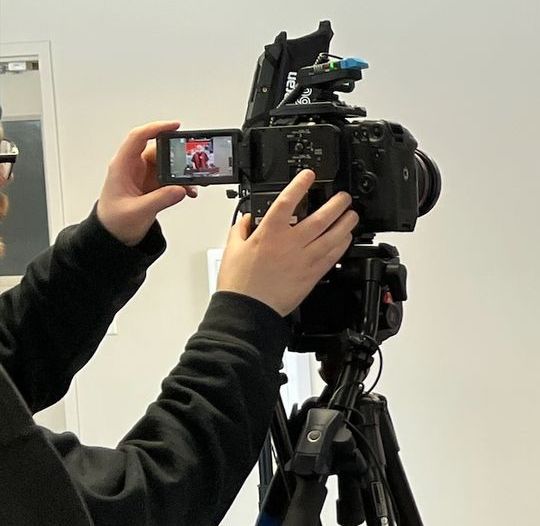
Last week on Tuesday, Perkins Media visited Smith Metal Products in Center City, Minnesota. They spent the day capturing what we do at Smith Metal Products, why our employees want to be here, and why customers like working with Smith. It is difficult to capture everything you want to say in a short video, but we are excited to see the end result. The video will be used on our website as well as in our tradeshow booths. Here are some things we are looking to communicate through the video: 1. We value our customers and work hard every day to make high-quality products. 2. Since we are employee-owned, employees have an ownership mentality that translates to deeply caring about the products and service we provide. 3. Smith Metal Products takes care of our employees, and they are able to grow wealth for retirement through the ESOP (employee stock ownership plan). 4. We make everything in the USA. By working with us, customers are supporting American jobs. In addition, customers do not have to worry about long overseas lead times, higher shipping costs, uncertain tariffs, and parts getting delayed in customs. 5. Collaboration is important to us. We like to be involved in the product development process early to provide feedback on design for manufacturing. We can describe how different features will affect the metal injection molding process and ways we may be able to save the customer money by removing the need for some secondary machining operations. 6. We are a metal injection molding (MIM) company. Not every part is a good fit for MIM. If we think that a potential customer's part design could be made better in a different way (due to wall thickness, lack of complexity, low volumes, etc.), we will be honest and communicate that. We want our customer to be happy and confident in the choice to work with us. Looking at the list above, we might need a couple videos, but we are excited for some fresh content. We are here and ready to collaborate! If you have a design that might be a good fit for MIM, email us at DFM@smithmetals.com Do you need video content for your business? Find out more about Perkins Media at www.perkinsmediagroup.com or email them at info@perkinsmediagroup.com
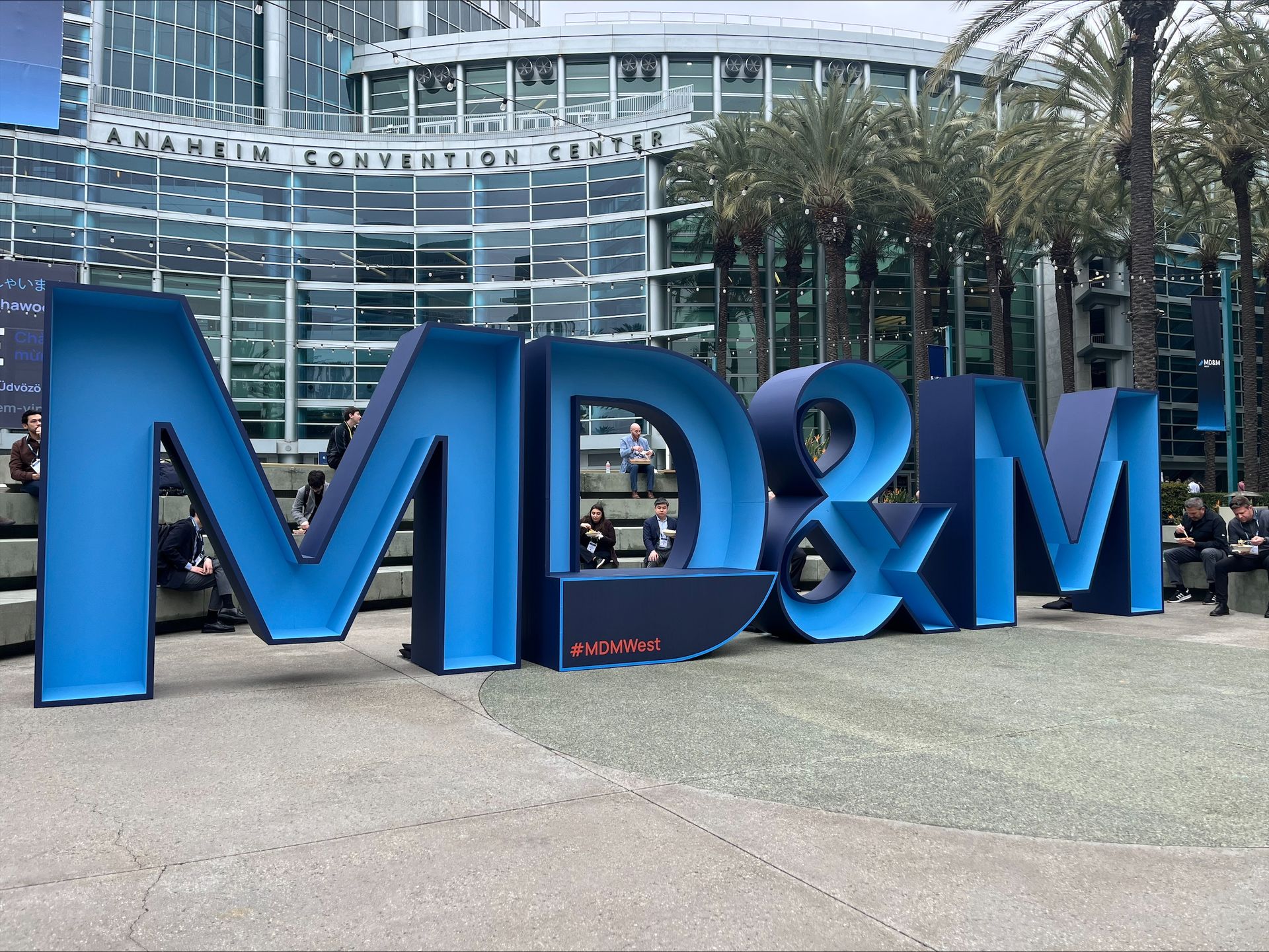
January and February were busy months for us. First, we attended the SHOT Show® in Las Vegas, Nevada at the end of January. There was a lot to see, and so many people to talk to with 14.1 miles of aisles within the two convention centers! That is a lot of ground to cover. Companies bring their newest products for all to view and connect with fellow companies in the shooting, hunting, and outdoor recreation space. The Smith Metal Products team was able to connect with current customers and discover potential customers as well. At the beginning of February, we traveled to Anaheim, California for MD&M West. This show was previously known as Informa Markets Engineering West. Under the name MD&M West, it now combines MD&M West, ATX West, D&M West, Plastec West, and WestPack. There are all types of manufacturers included in the 1700+ that attend this show. Most of the companies that we interacted with were in the medical device space. There were over 13,500 attendees. Some of the people that stopped by the Smith Metal Products booth were not familiar with metal injection molding, so we had the opportunity to educate some people as well. Hopefully, they will take what they learned and incorporate it into designs they are working on. At both shows, it was fun to talk to companies about their designs and how we can help them. We were thankful to receive a lot of interest and explain why Smith Metal Products is a vendor that can help make a design a reality. Until next year!
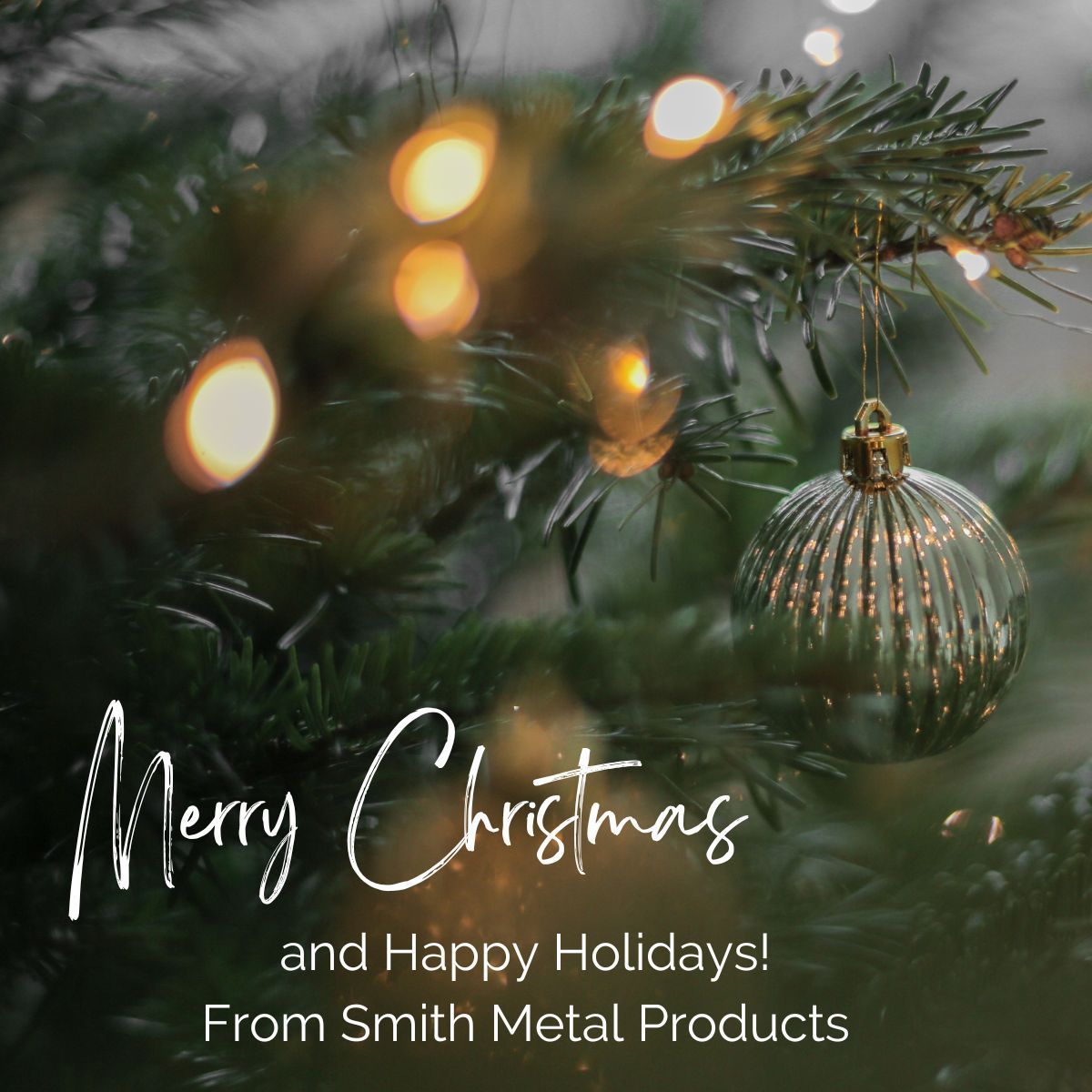
Merry Christmas to those that celebrate. Smith Metal Products is closed tomorrow, December 24, and Wednesday, December 25 in observance of the Christmas holiday. We will return to the office on Thursday, December 26, ready to collaborate with you. Hopefully, you get some time to relax and spend time with friends and family. Happy Holidays!
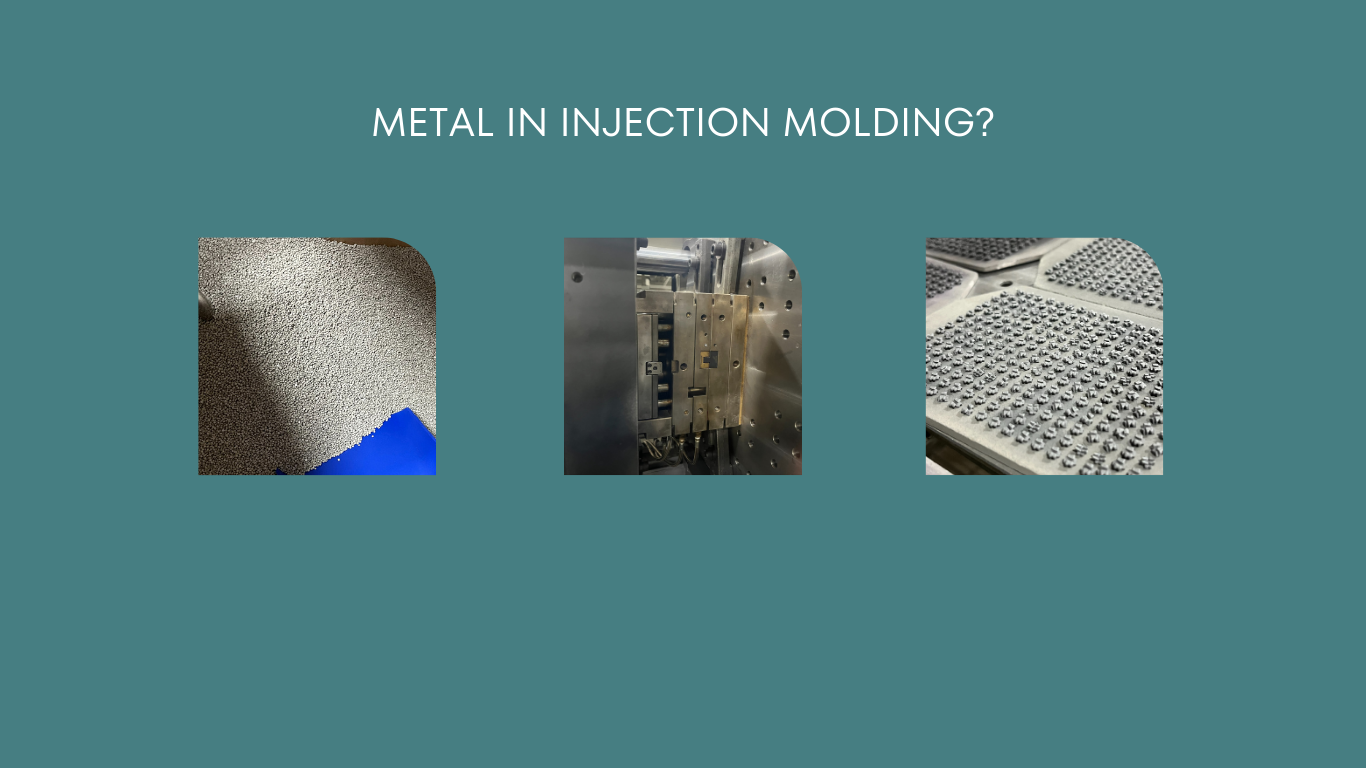
The answer is yes and no. Yes, metal can be used in injection molding, but not by itself. In order to get the powdered metal to take the shape of the mold and hold the shape, about 20% of plastic is added to approximately 80% powdered metal. These pellets are called feedstock and they are melted and pushed into the mold. After this point, the part is not complete like it may be with plastic injection molding. The metal part needs to go through the debinding process in order to remove all of the plastic. You cannot leave the part alone after debinding, because it is very fragile and you can think of it like a sandcastle like structure. Then the metal parts go through the sintering process to strengthen the part and remove the holes that were left behind by the plastic. We most commonly use stainless steel powder. Titanium is another metal that we commonly work with. There are some metals that are not compatible with our process. We do not use aluminum, zinc, brass, magnesium or copper in the metal injection molding process. If you want to learn more about the whole process, see the "What is MIM?" section of our website.