Smith Metal Products Blog
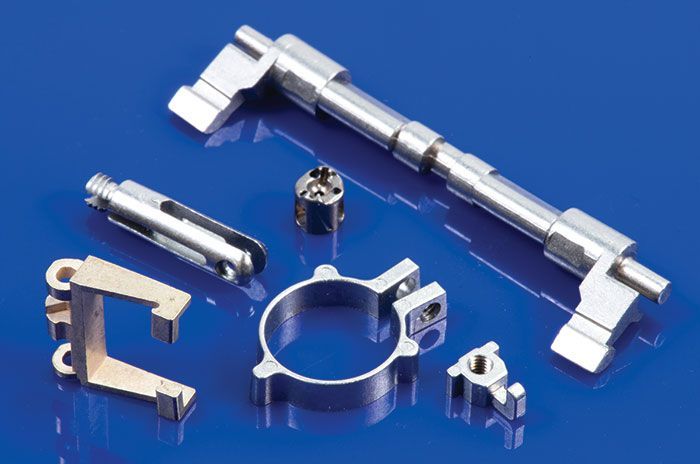
Pivot point components used in a wide range of medical grasping instruments are precisely manufactured using the metal injection molding process (MIM) from Smith Metal Products.
Pivot point components provide natural dexterity in grasping forceps, retractors, needle drivers and similar advanced medical instruments. These critical pivot point components are precisely manufactured using the metal injection molding process (MIM) provided by Smith Metal Products.
The pivot points pictured measure 0.50″ x 0.1875″ x 0.25″ and have tolerances of ±0.0015″. Part features included undercuts, parallel holes and perpendicular shafts – all produced accurately with Smith MIM process. These net shaped MIM produced components required no machining saving both material and machine time.
The pivot point design makes possible unique two-bladed instruments with a specific medical function. For example, grasping fine tissues, suturing with tiny needles, dexterity to perform surgical, obstetric and dental procedures. These two-bladed instruments are designed in many configurations with a handle for manipulating, compressing and grasping motions — all made possible because of the pivot point components robust design versatility.
Smith Metal Products MIM process manufactures these pivot point components to close tolerances with extra durability so the instrument functions reliably with repeatable accuracy. Smith Metals provides a better solution over similarly configured components that require complex precision machining. By metal injection molding 7-4 or 316 stainless steel, the pivot point components pictured meet the quality and durability requirements for these grasping instruments.
MIM is often a preferred process to achieve small precision medical device components. That’s because MIM parts are pre¬cise, net-shaped and can be produced faster than machining and usually with no secondary operations. If a high tolerance needs to be held and cannot be entirely MIM molded, Smith uses CNC machining equipment to achieve tighter specifications while still being more competitive than complete machining of parts.
Parts that are suitable for MIM processing include those that have complicated geometries in annual volumes of 10,000 pieces or more and a finished part weight of less than 100g (3.5 oz). All dimensions of the component should be 3 in. or less, and the maximum wall thickness should be 3 mm (0.125 in.) or less.
Request a quote, Part Evaluation, or call us today at 651-257-3143.
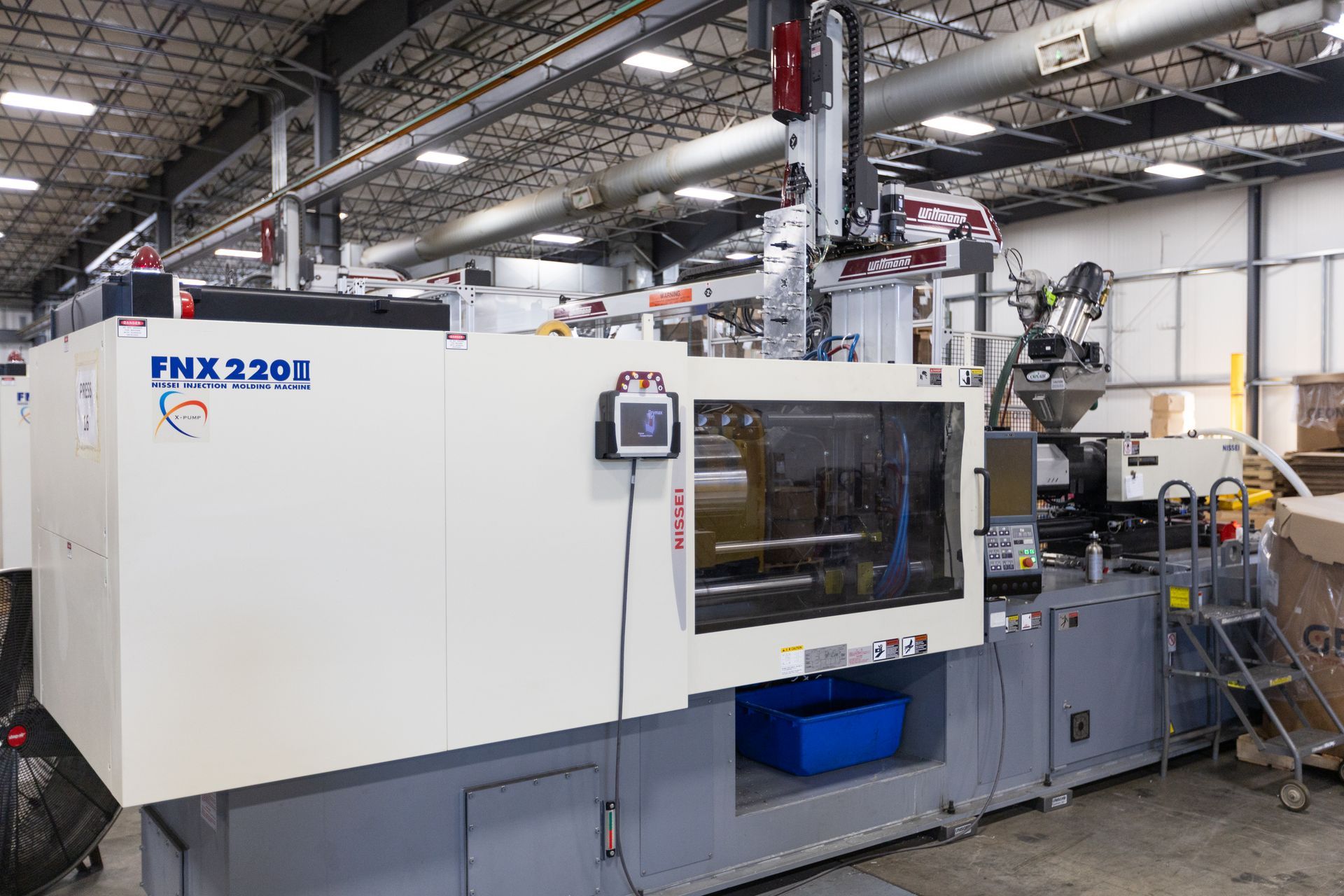
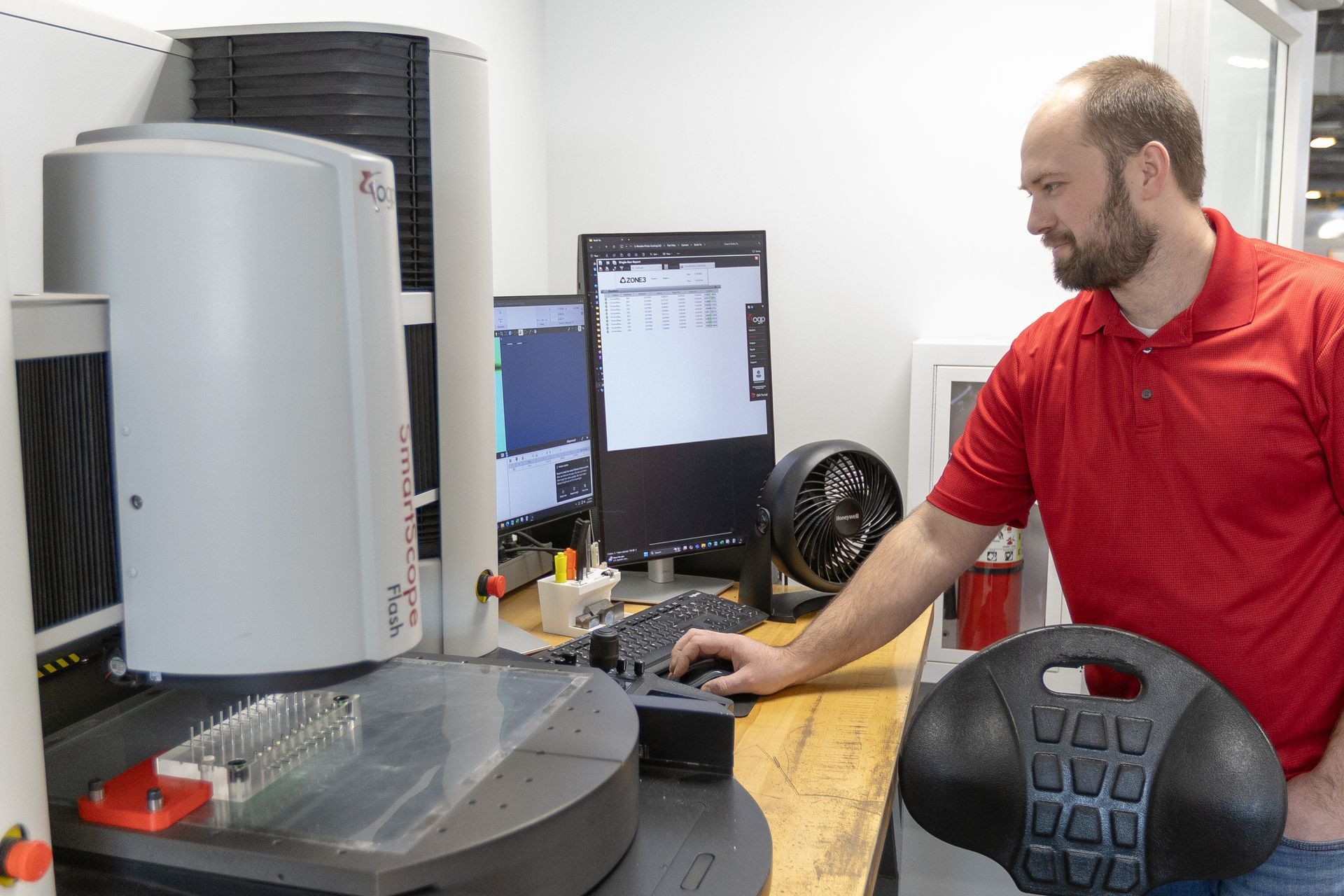
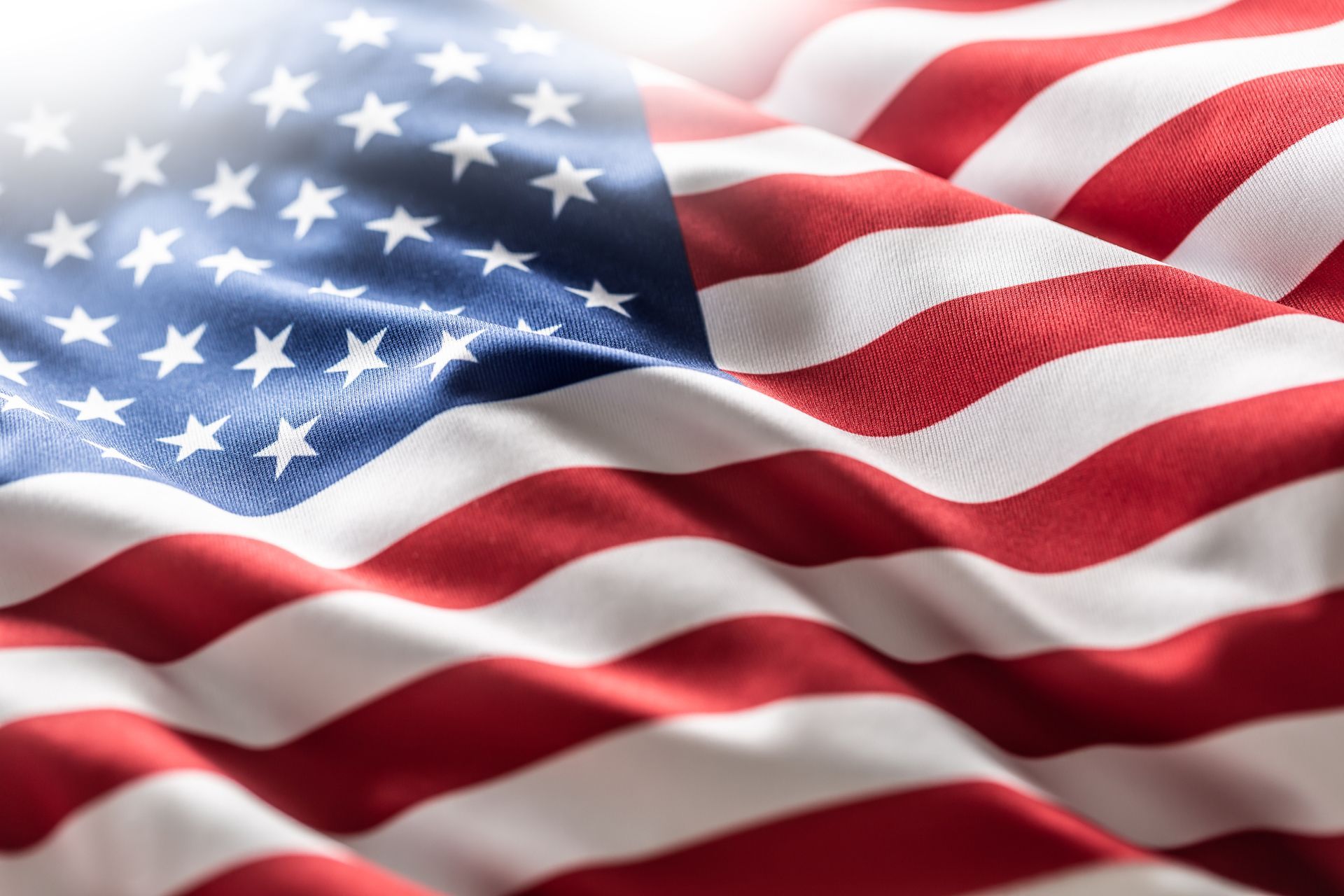
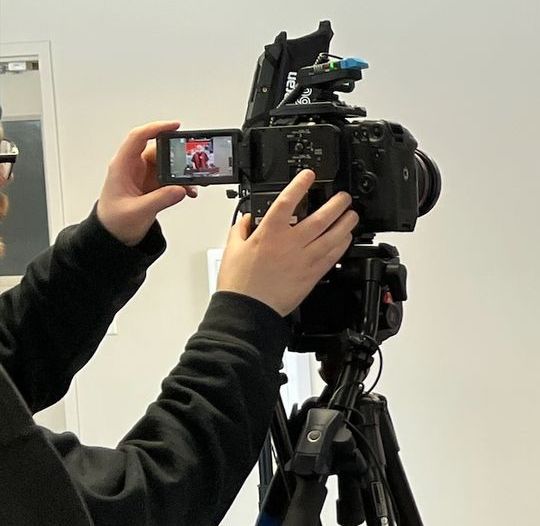
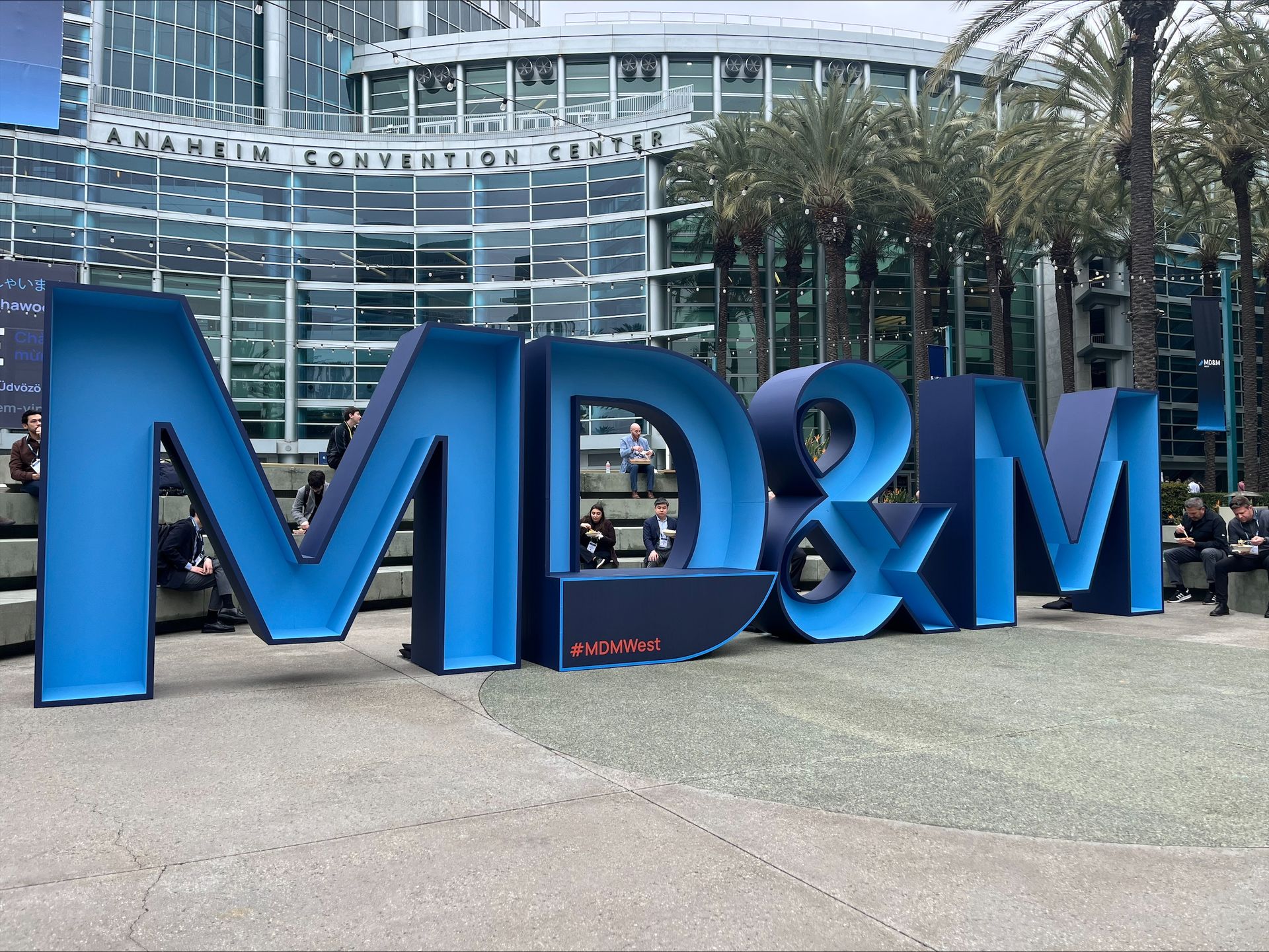
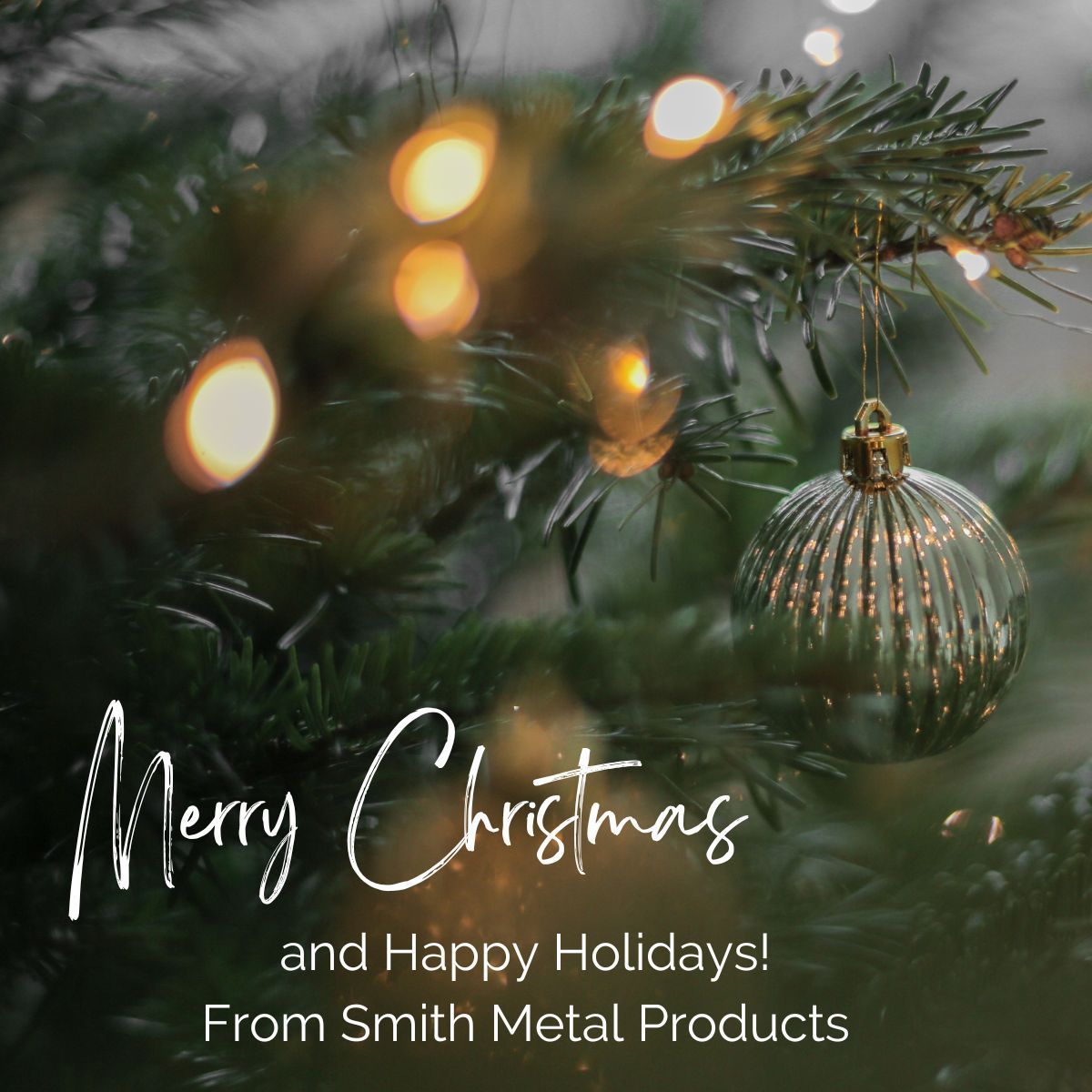
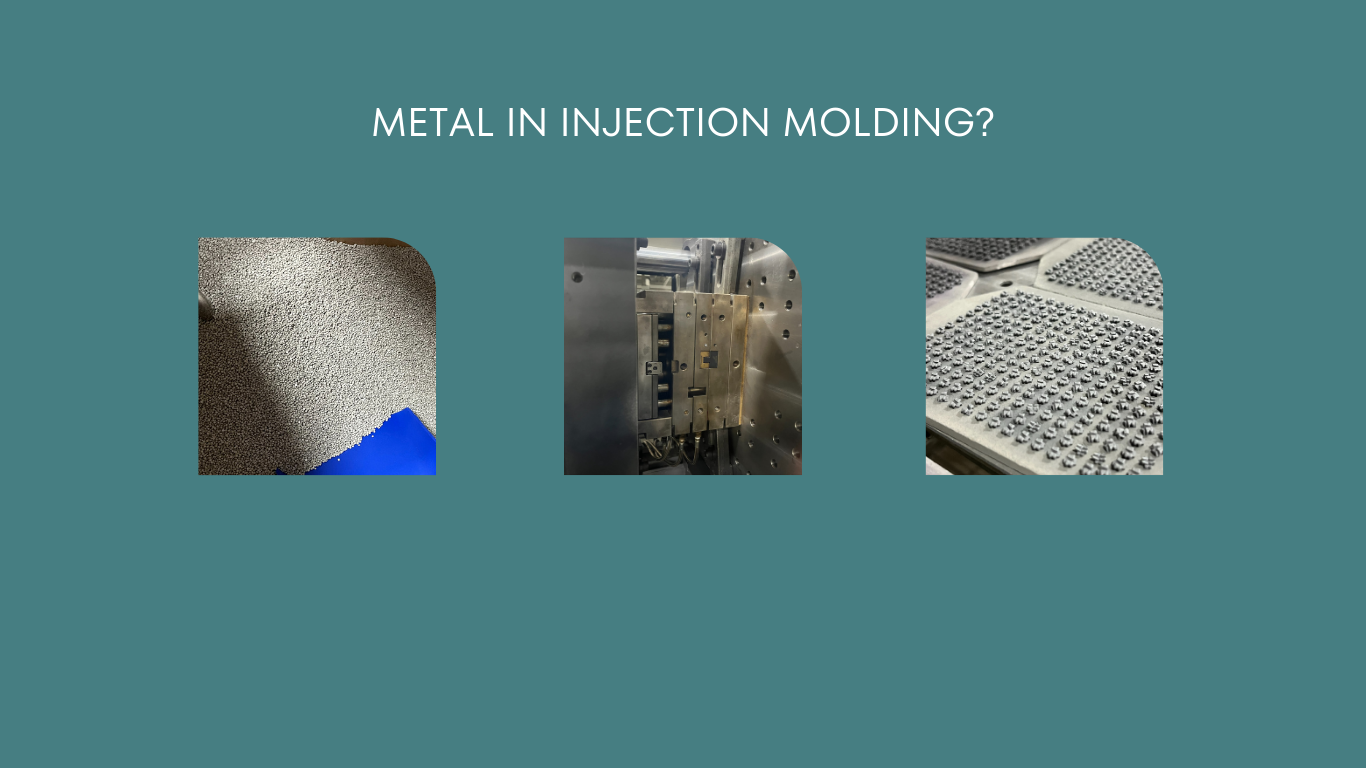