Smith Metal Products Blog
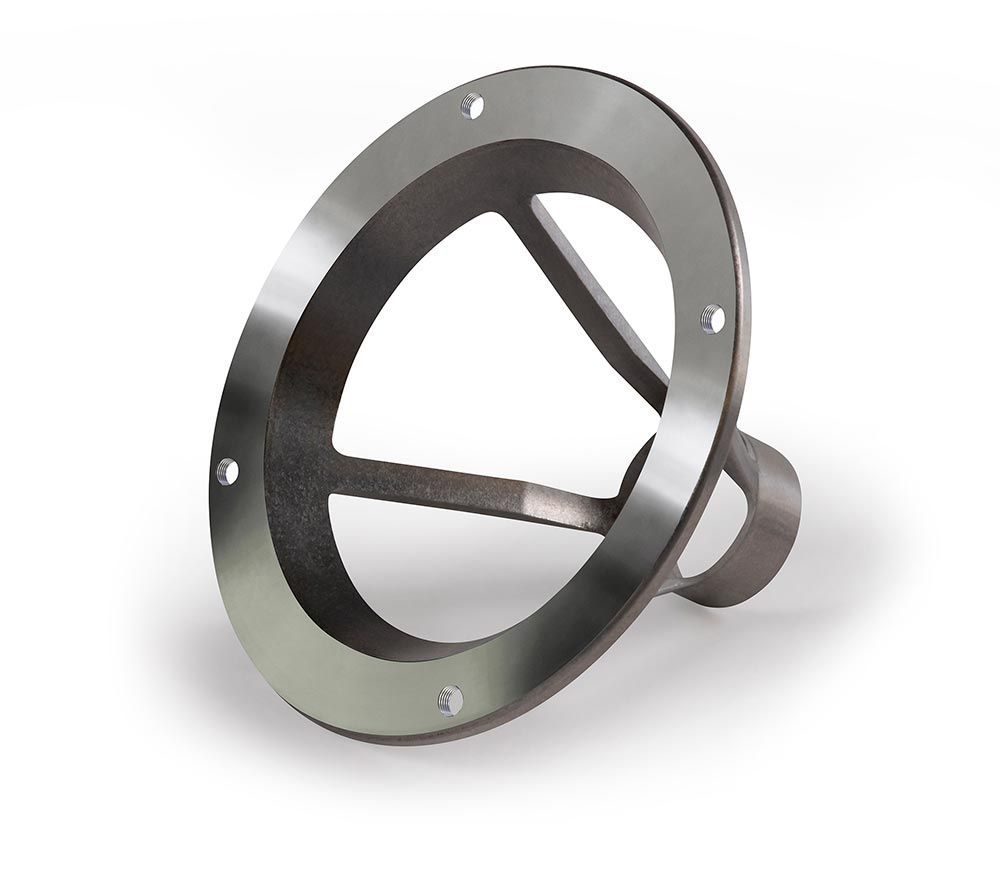
Smith Metal Products adds CNC lathe to in-house machining capabilities making Smith one of the largest MIM molders with significantly more CNC machines and advanced secondary processing capabilities in the USA. Smith Metal’s machining capabilities include CNC 5 axis machining, CNC turning, coining, laser etching/engraving now with 12 in-house machine tools, CNC machinists and CNC programmers. Smith also has established external sources for polishing, lapping, grinding, and EDM wire cutting.
Smith Metal Products calls it their MIM Hybrid Solution for taking MIM net shaped parts beyond the common achievable MIM molding tolerances, stated Jim Beyer Account Manager. “We’ve seen a big increase in interest for MIM parts requiring fine tolerances which are beyond MIM molding capabilities. Secondary, post-process machining is often needed to produce these very precise round holes, threaded holes and smooth, flat surfaces for interfacing with other parts.”
MIM is often a more effec¬tive process to achieve precision parts while eliminating machin¬ing because MIM parts are pre¬cise, net-shaped parts that are produced faster and usually with no secondary operations. If higher tolerances need to be held and cannot be MIM molded, Smith’s MIM Hybrid Solution to achieve tighter specifications is utilized while still being more competitive than complete CNC machining of parts.
Smith Metal Products produces MIM parts for a variety of industries including: automotive, aerospace, firearms, medical, dental, recreation and appliance. Materials available for MIM molding range from stainless steel, steel, titanium, and include most all ferrous materials. Parts that are suitable for MIM processing include those that have annual volumes of 25,000 pieces or more for a single component, or 3 or more parts that have annual usage of 10,000 or more and a finished part weight of less than 100g (3.5 oz). All dimensions of the component should be 3 in. or less, and the maximum wall thickness should be 3 mm (0.125 in.) or less or can be cored out to have thinner wall sections. Smith will help you fine tune your designs to improve manufacturability and reduce costs. MIM parts must be ferrous metals.
Smith Metal Products operates a state-of-the-art 65,000 square foot facility that is ISO 9001:2008 Certified and ISO 13485 compliant. The company’s controlled documentation system assures customers of consistent set-up and repeatability on every production run. A quick-turn 3D Binder-Jet Metal Printing process is also available for customers to evaluate and verify their product run utilizing a MIM-like process without the cost of building a test mold.
Request a quote, Part Evaluation, or call us today at
651-257-3143.
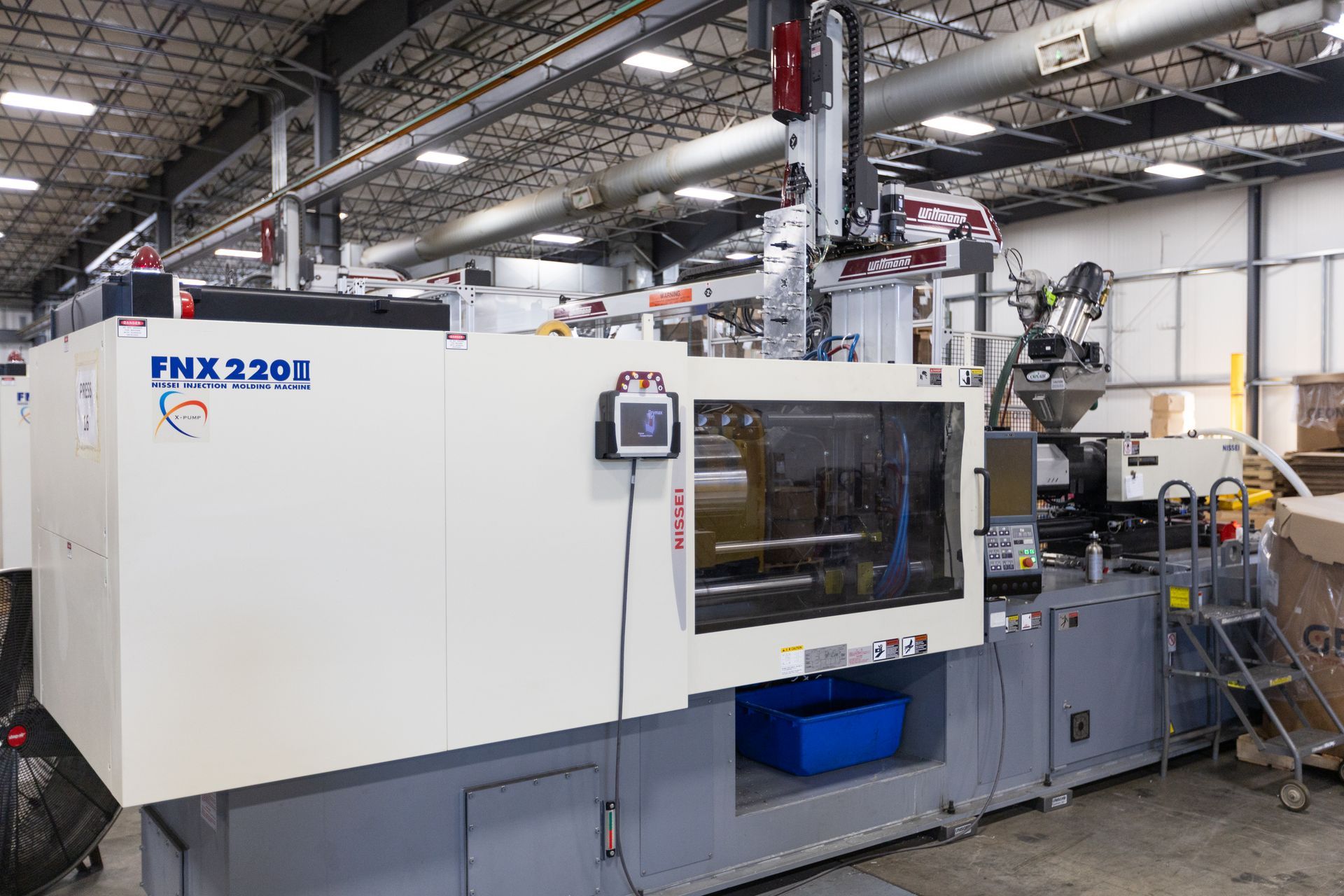
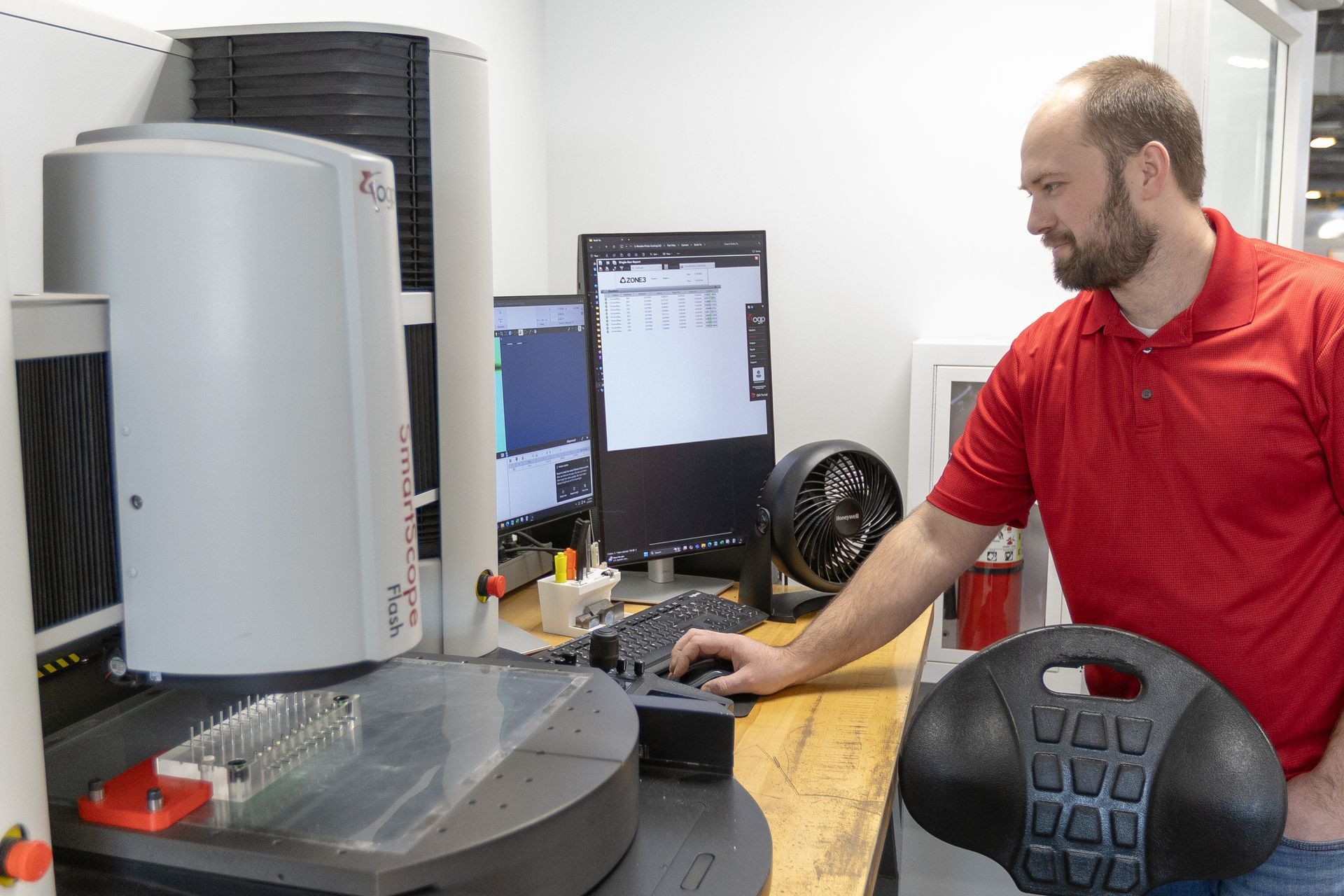
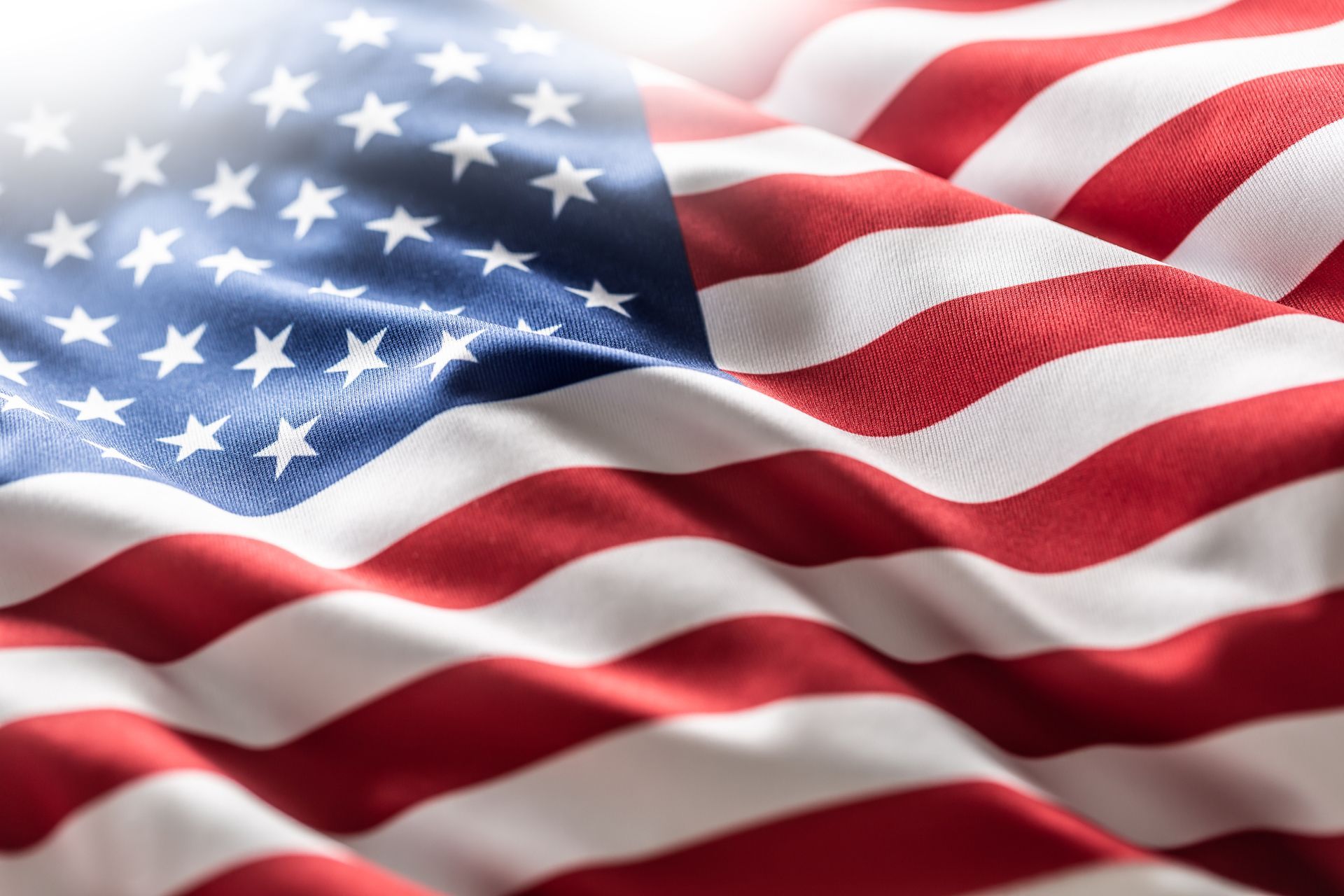
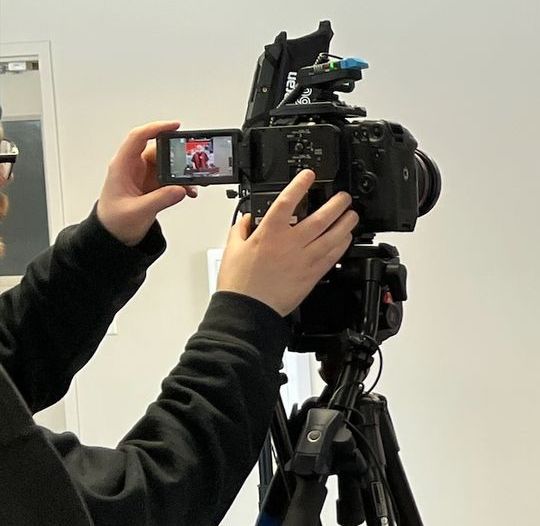
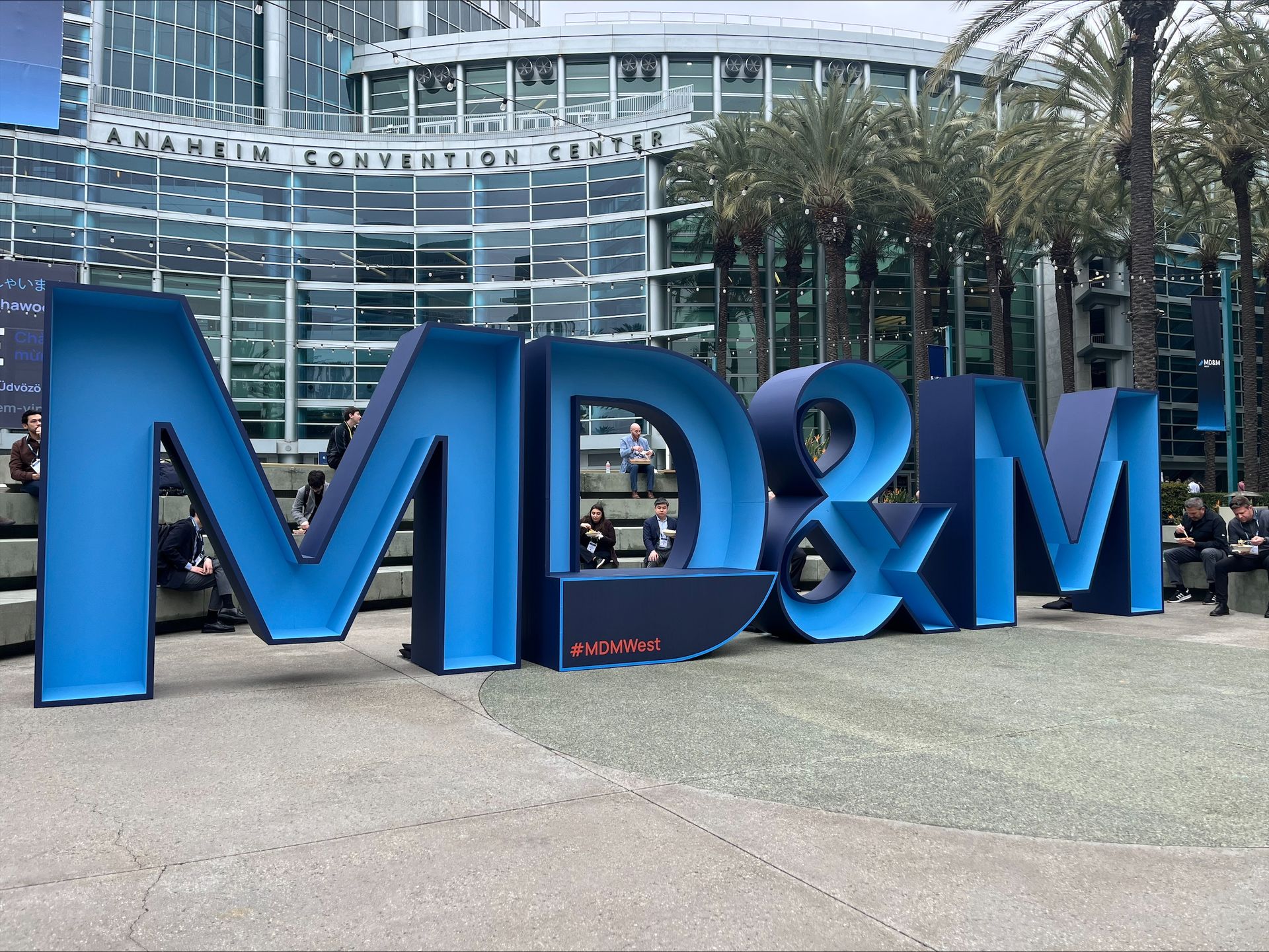
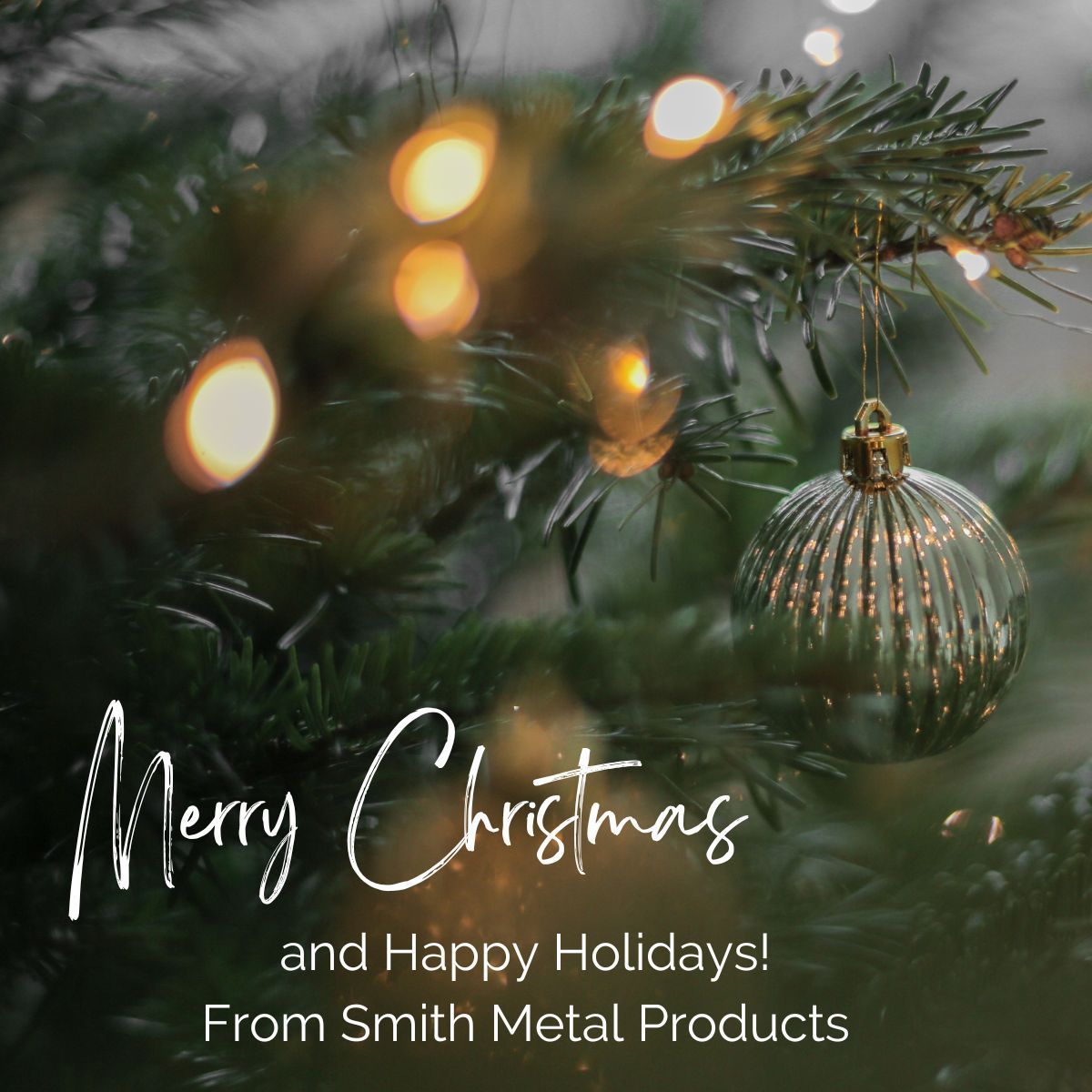
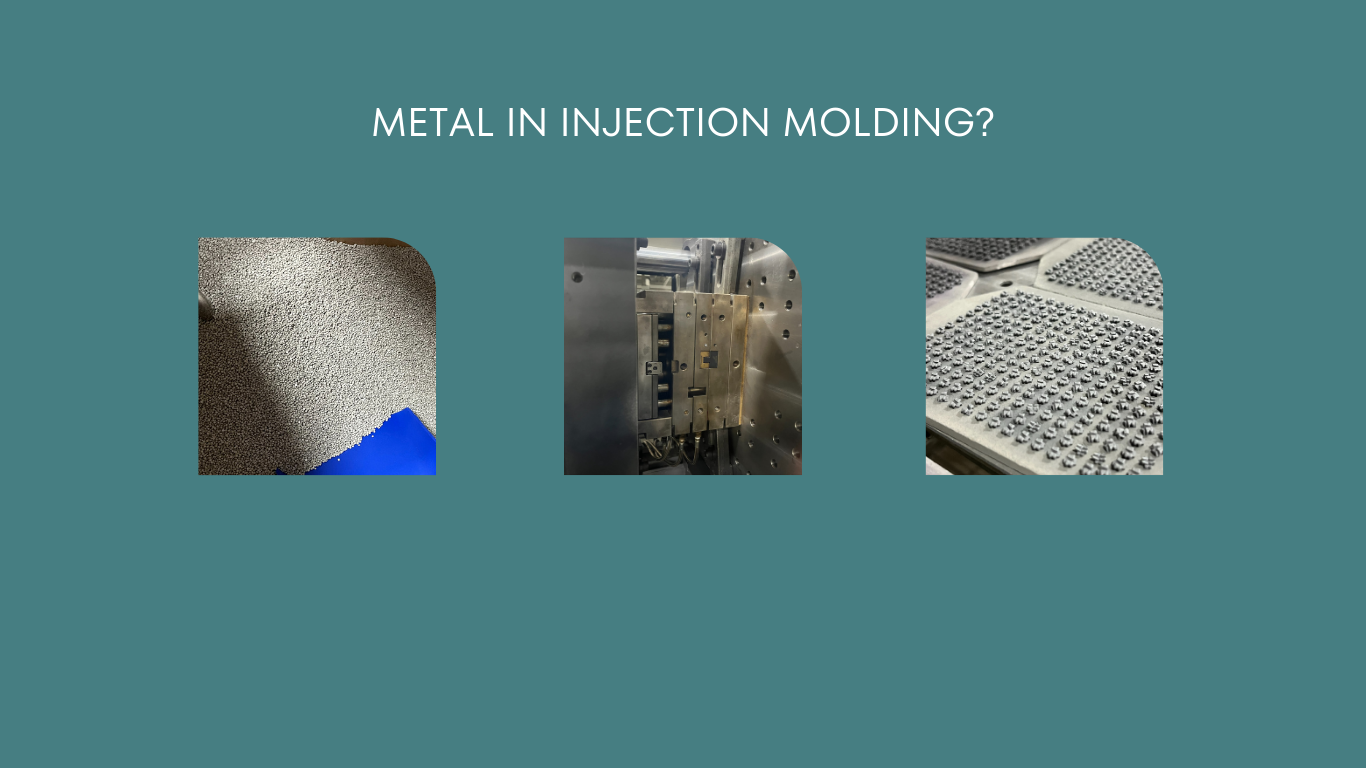