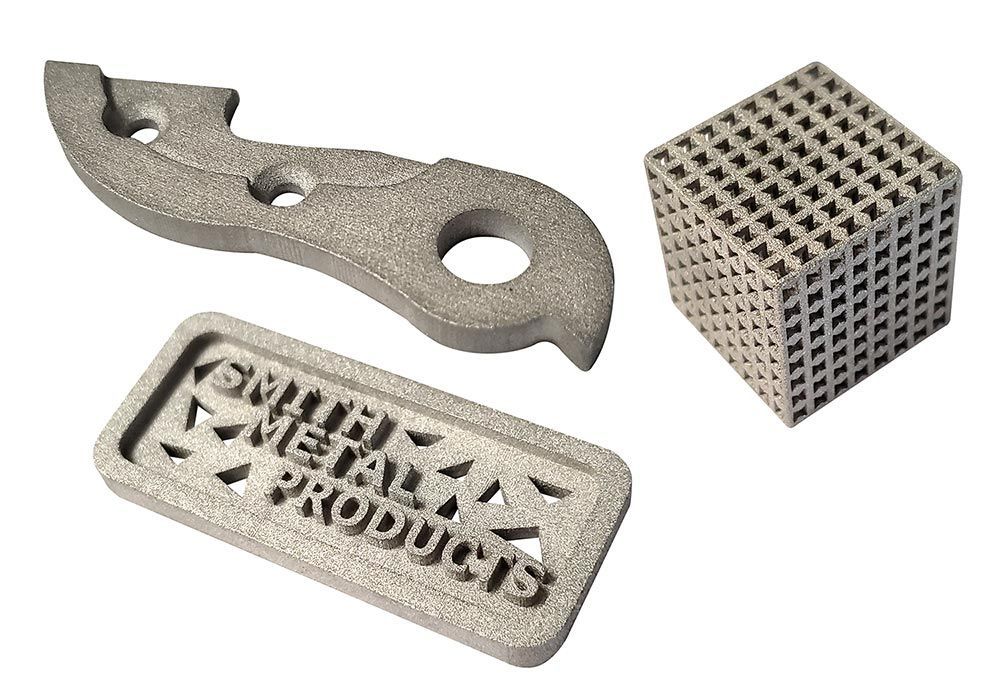
Smith Metal Products adds quick-turn 3D Binder-Jet Metal Printing parts for customers to evaluate and verify their product run utilizing a MIM-like process without the cost of building a test mold. Now manufacturers can easily see, touch and evaluate comparable prototype MIM-like parts produced on Smith Metals advanced 3D Binder-Jet Metal Printing additive production system.
Smith Metal’s 3D Binder Jetting is the only form of metal powder 3D printing where a part is fully formed before thermal energy is used to sinter or fuse the metal particles. This ensures that the final part’s micro-structure is correct to obtain high quality functional and performing parts. Binder Jetting uses a liquid binding agent and is sprayed onto a thin layer of powdered metal particles. Repeating this one layer at a time, the resulting prototype parts are then cured and sintered at high temperatures, creating the final part. Just like Smith Metals MIM parts, 100 percent of the binder is removed during the sintering process.
Smith Metal reports that printing prototype parts is faster and more versatile versus producing expensive test molds for metal injection molding or CNC machining costly prototype parts. Lead time for these prototypes is reduced substantially and allows customers to make adjustments quickly before the final MIM mold is established. 3D printed prototype parts give customers added confidence for their designs with successfully manufactured parts.
Smith Metal’s new 3D Binder Jet Metal Printing capability is designed to support a customer’s research and development efforts with a bridge to MIM molded parts. This new capability is especially desirable for reducing time-to-market developmental programs. In addition to not requiring time-consuming and expensive mold building to evaluate MIM parts, the new process can eliminate and/or significantly shorten lead time from R&D into full volume production.
Available part materials for this new prototype capability include all those available in Smith Metals standard MIM offering. These include low-alloyed steels, stainless steel, most ferrous metals and titanium.
Available part sizes range up to 3 inches long by 0.25 inches thick and weigh up to 100 grams. A Smith Metals Expert will be happy to provide free basic Design for Manufacturability (DFM) recommendations to help you optimize your part designs for MIM production. MIM achieves medium to complex metal parts quickly while eliminating extensive machining. Parts suitable for MIM processing include those that have annual volumes of 10,000 pieces up to several million. Finished parts are net shape accurate with in-house finish machining available for closer tolerance features. Ideal MIM part candidates include firearms, defense, medical, dental, orthodontics, computer, aerospace automotive, appliance and recreation applications.
Request a quote, Part Evaluation, or call us today at
651-257-3143.
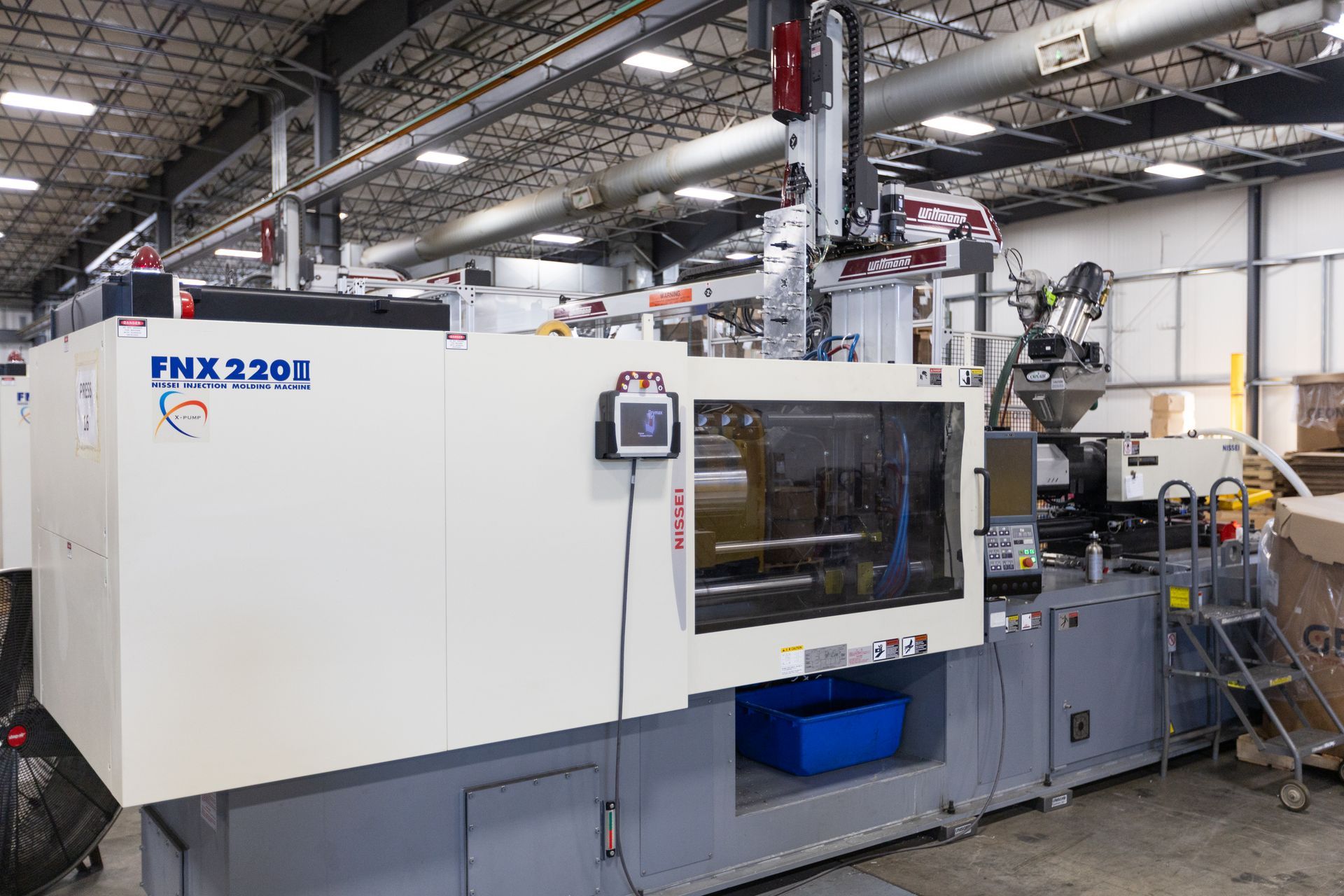
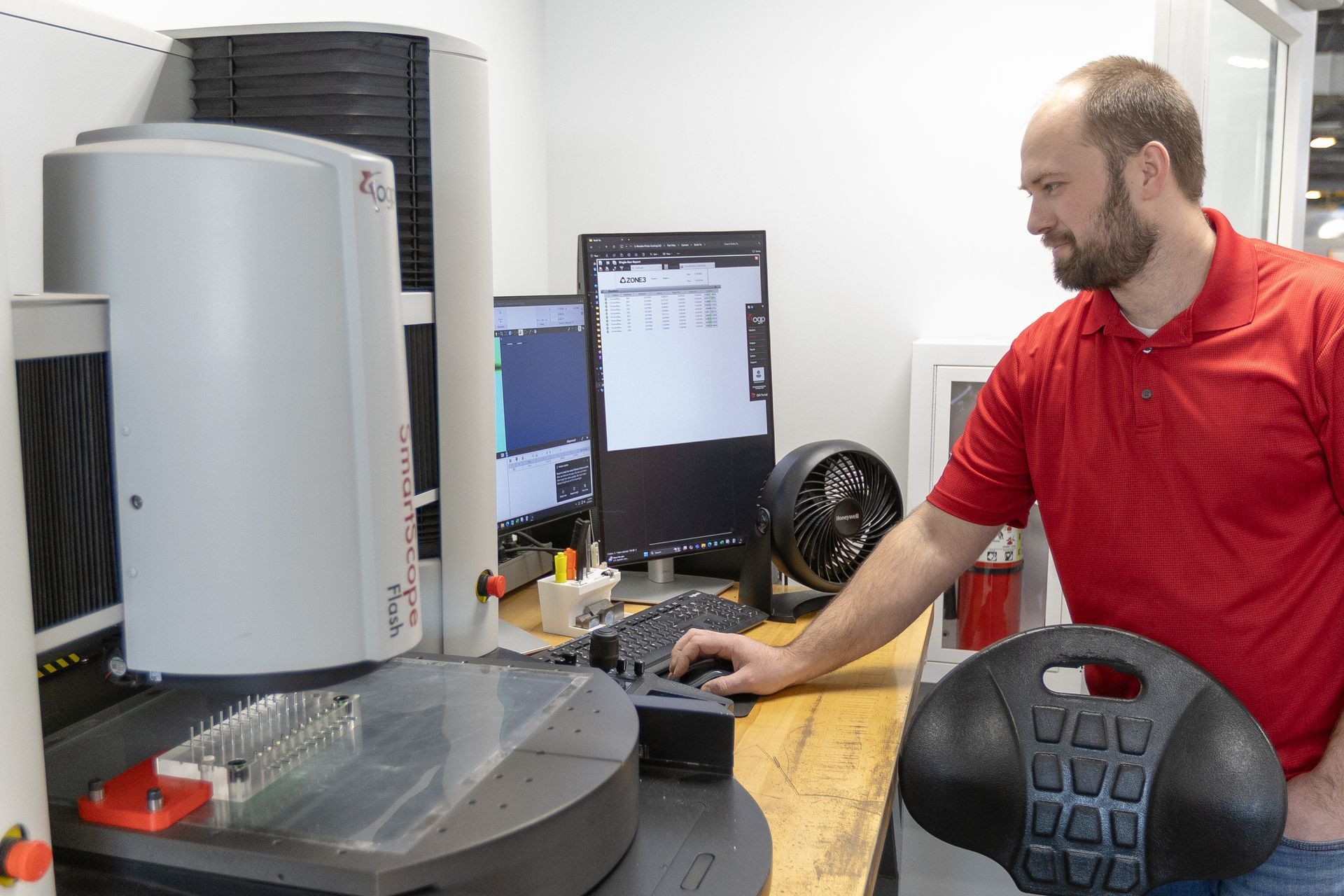
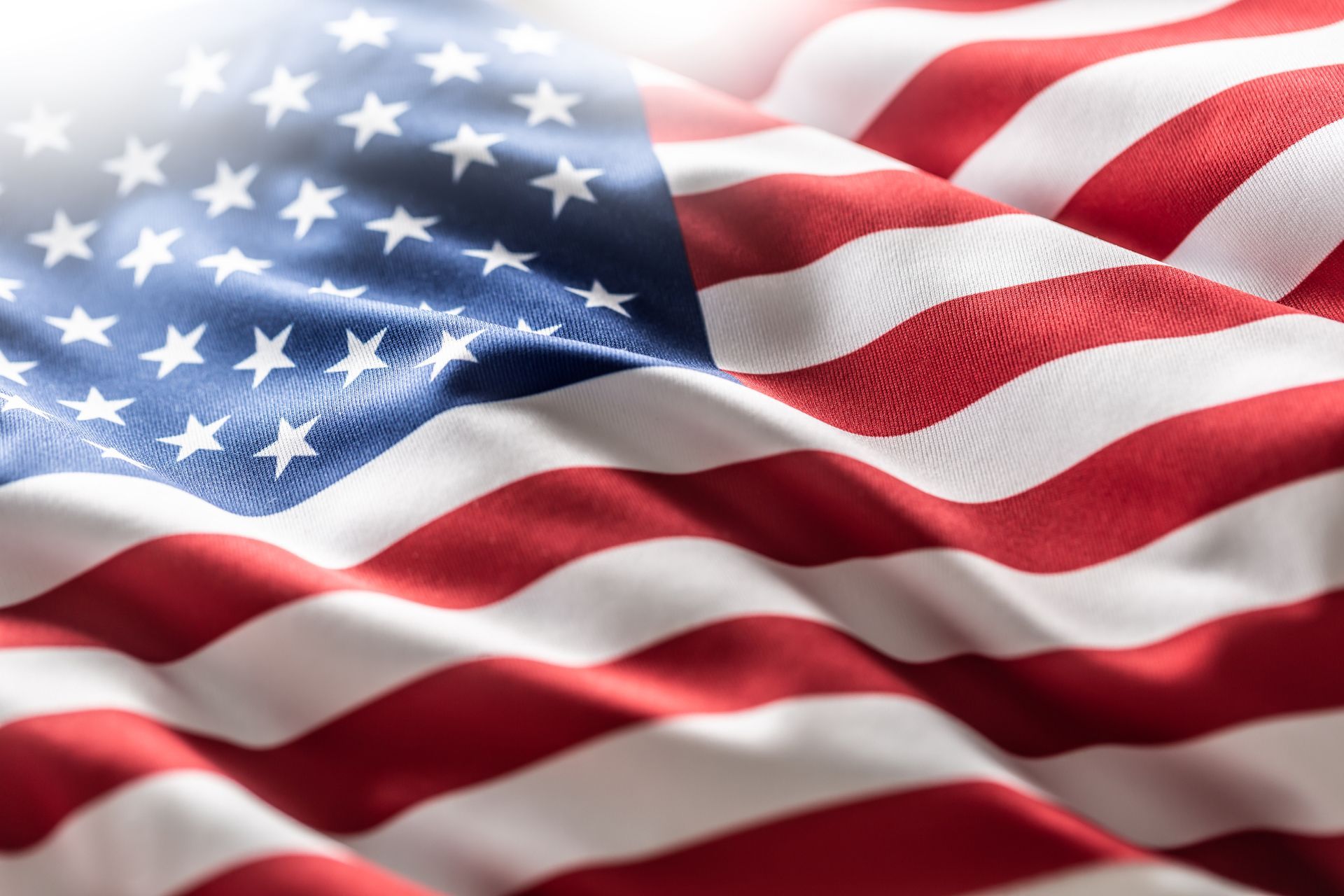
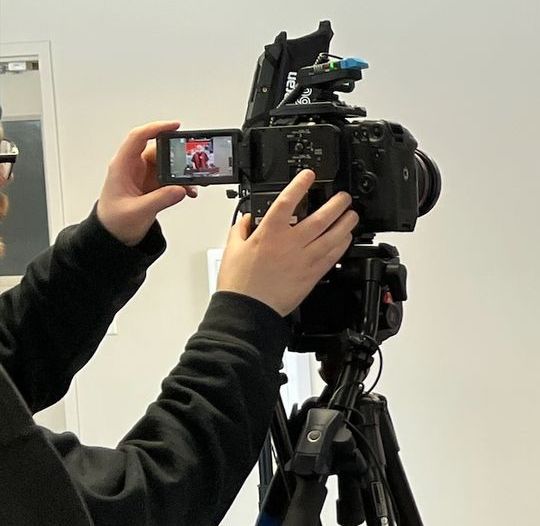
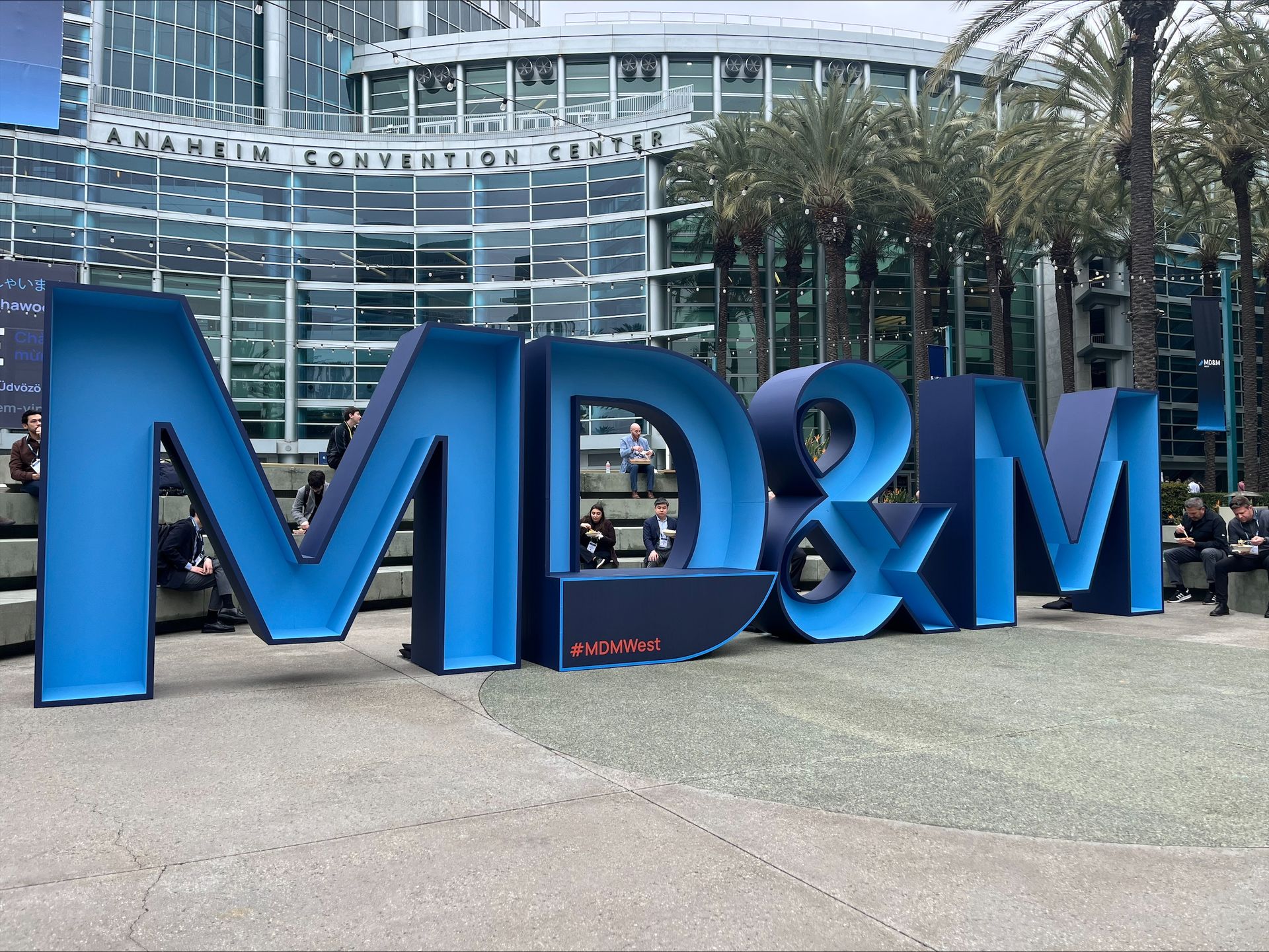
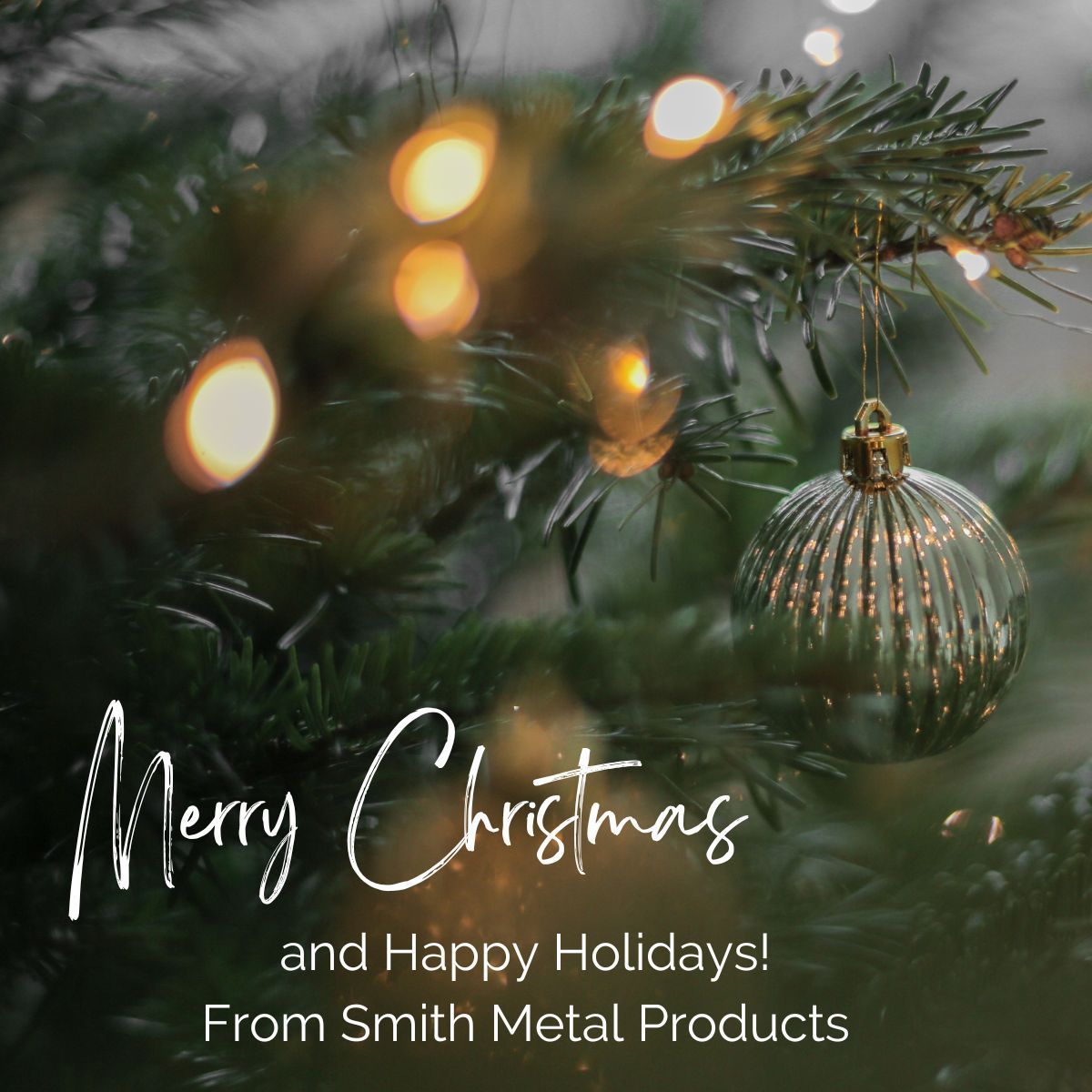
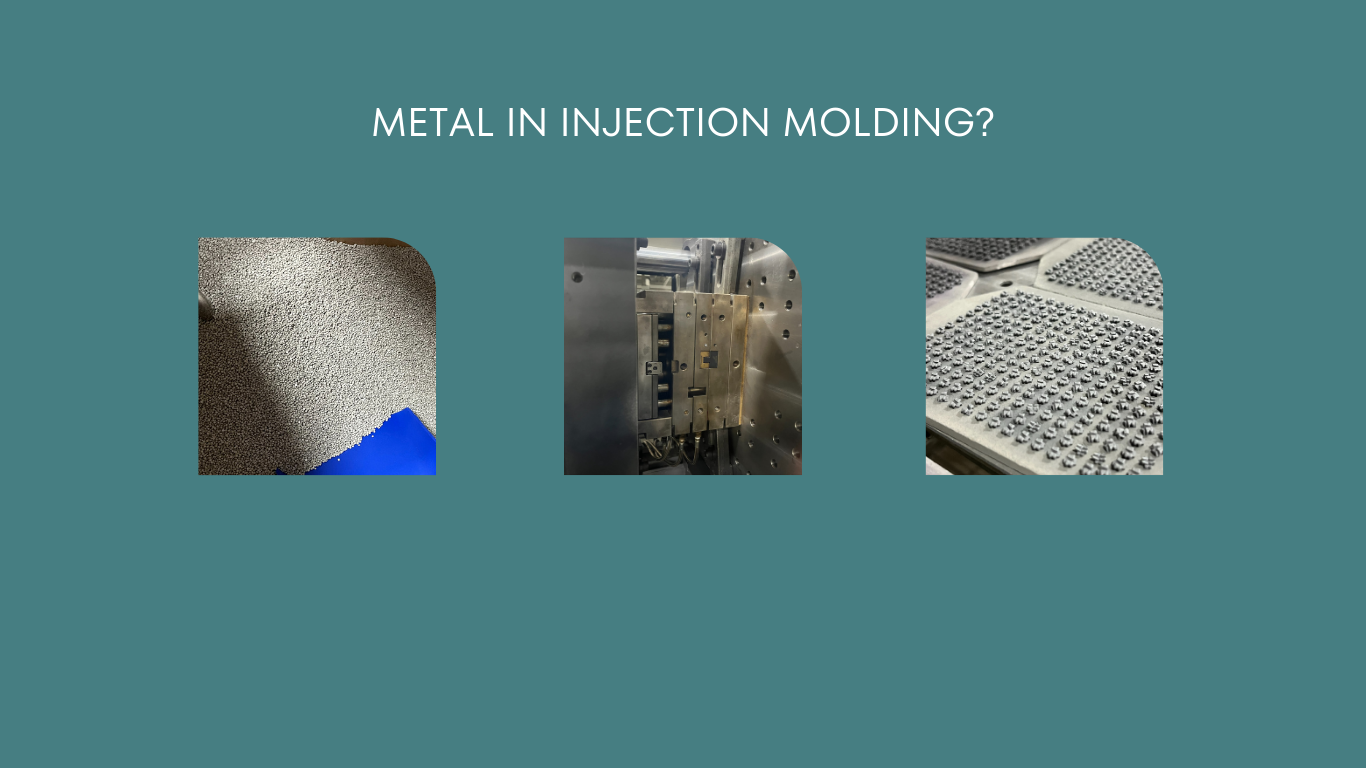